PROBLEM:
Traveling can often be stressful, especially if you are traveling with multiple pieces of luggage. One hands-free solution is the auto-following smart suitcase. Already available on the market, these suitcases cost upwards of $700 for a brand new suitcase. What about your perfectly good luggage at home?
SOLUTION:
For my senior capstone project in electromechanical systems design in Spring 2021, I designed and built a modular autonomous suitcase attachment, or MASA, to fill the gap in smart luggage products. With a team of four other students, I created MASA to be cheap, lightweight, and modular to fit varying suitcase sizes, all while fulfilling four core functionalities:
1. Easy mounting and strong clamping
2. Following in 2D at walking speed
3. Object detection and avoidance
4. Wheel retraction for manual mode
Over the course of the spring semester, we accomplished these goals with a successful final prototype of our smart system. MASA was awarded "Best Overall Project" at the 2021 MechE Design Expo and "Most Innovative Design" at the 2021 TechSpark Design Expo, where we competed against several other multidisciplinary capstone teams.
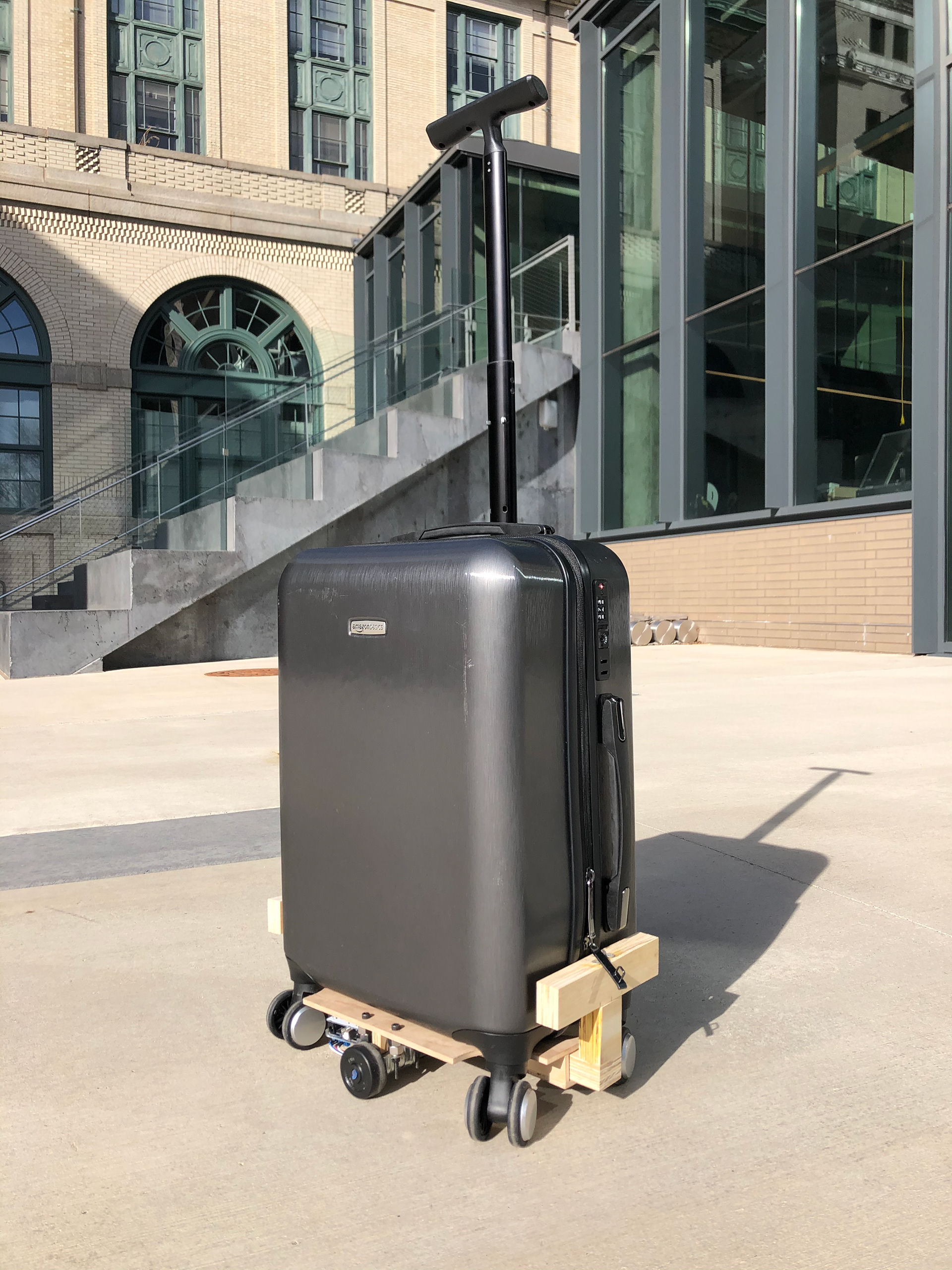
MASA mounted on a carry-on suitcase
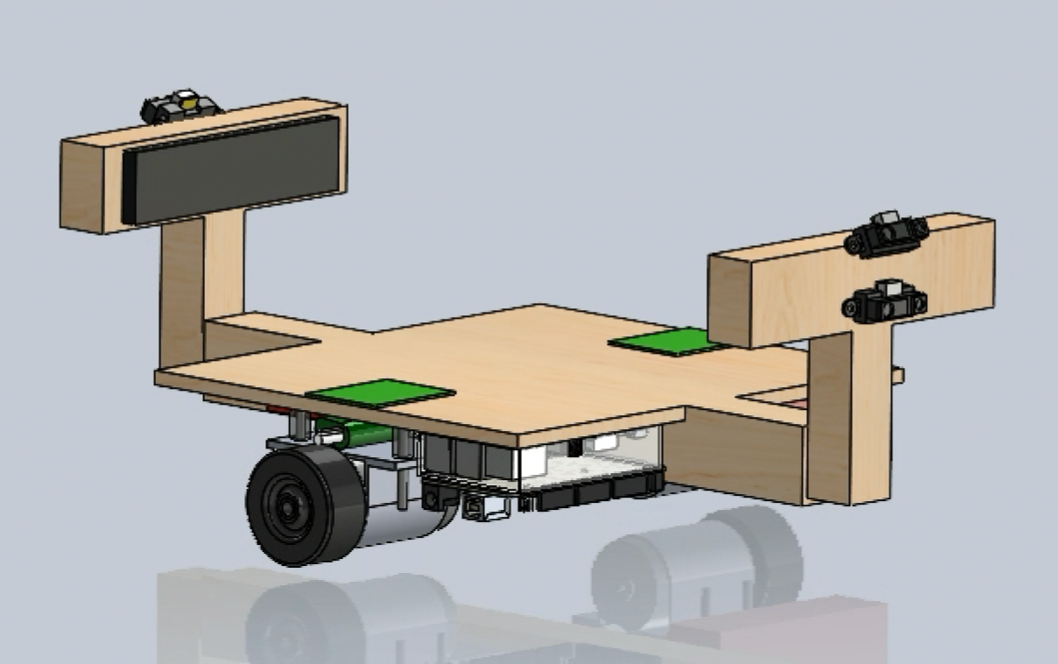
Final CAD model of MASA
MY CONTRIBUTIONS:
As the Design Lead of my team, I was heavily involved in the initial ideation, design, and prototyping phases of our process. Specifically, I focused on the mechanical subsystems, like building the wooden mount and spring-loaded clamping arms in the wood shop, and designing and testing the retractable wheel system. I also created all Solidworks models of our prototypes, and conducted multiple FEA simulations during testing. Finally, I managed our project timeline and kept my team on track to meet our weekly goals and project deliverables.
MASA: FINAL PROTOTYPE:
MASA is inherently an electromechanical device, utilizing sensors and actuators controlled by microcontrollers, all housed within a modular mounting system. Below is an overview of all the main components of MASA, which we can categorize into three critical subsystems: mechanical, electrical, and computational.
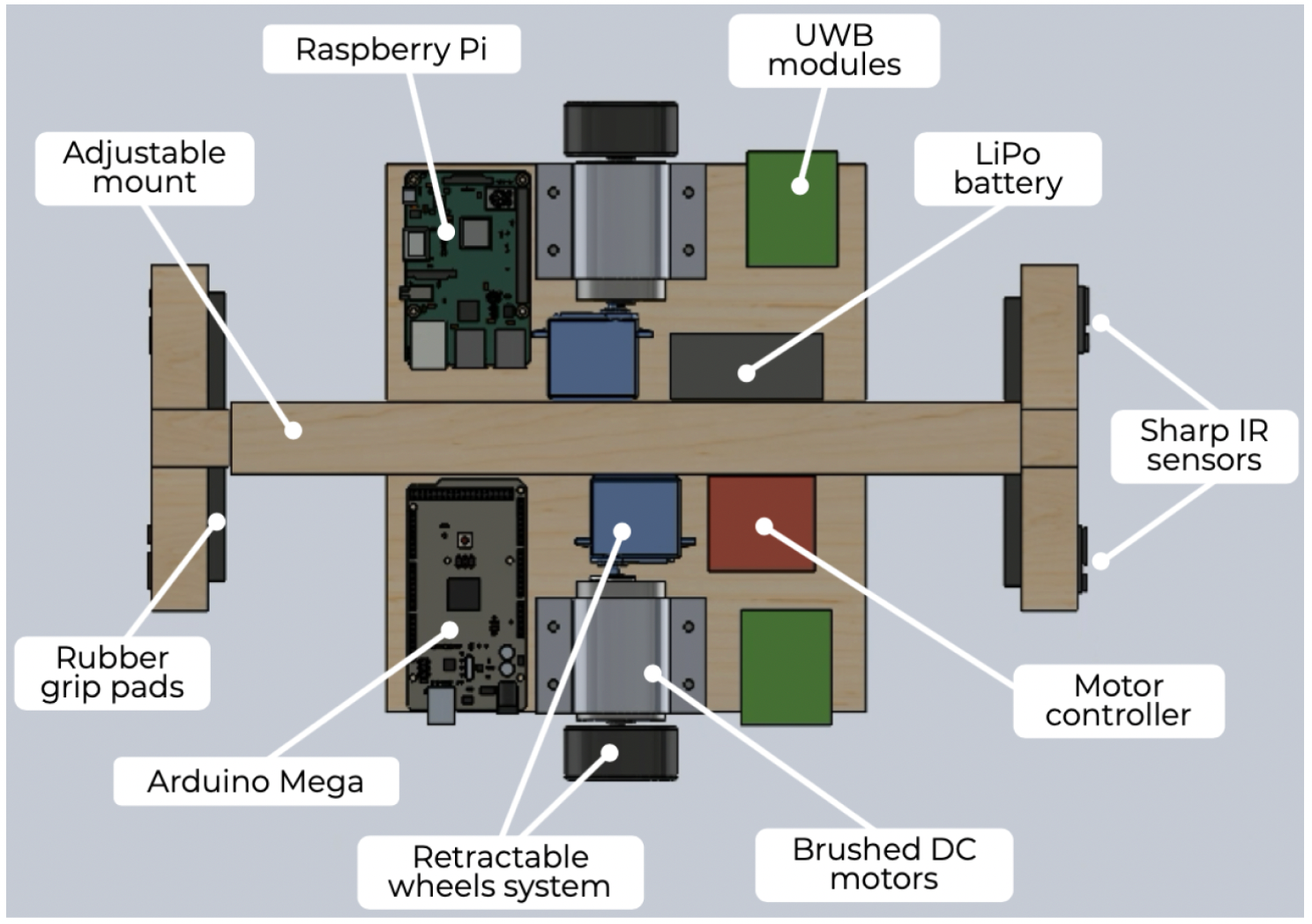
Overview of all final components
MECHANICAL
The main body of our modular mount is wood, which is lightweight, durable, and ideal for prototyping. While most of the components are attached on the underside of the mount, the wooden T-shaped clamping arms are connected by a pre-tensioned spring running inside the body. These spring-loaded arms provide a strong clamping force for our mount to attach to any type of suitcase. Here's how it works:
Video of spring-loaded clamping arms
ELECTRICAL
To move MASA in 2D, we use differential drive; two high torque, high RPM gearmotors each connect to a wheel to drive our system, which is balanced by the passive wheels of the suitcase. These DC motors are powered and controlled by a high amp Roboclaw motor driver. We also use four sharp IR sensors, two each on the front/back sides of MASA, to detect any obstacles in its path.
We also designed a retractable wheel system, which retracts the two driving wheels of MASA and allows the user to manually pull their suitcase whenever they choose. Due to the limited area underneath a suitcase, we decided to use a compact cam + servo mechanism to retract and engage MASA's wheels. The video below shows this vertical movement.
Lastly, we use a 14.8V LiPo battery to power our entire system, which can keep MASA running continuously for about 24 hours before needing a recharge.
Video of wheel retraction motion
COMPUTATIONAL
For 2D localization and detection of user heading, we utilize ultra-sideband (UWB) technology. With two UWB modules (tags) on either side of MASA and one UWB beacon (anchor) on the user, we are able to triangulate these points and determine the distance from and heading angle to the user. The diagram below shows this:
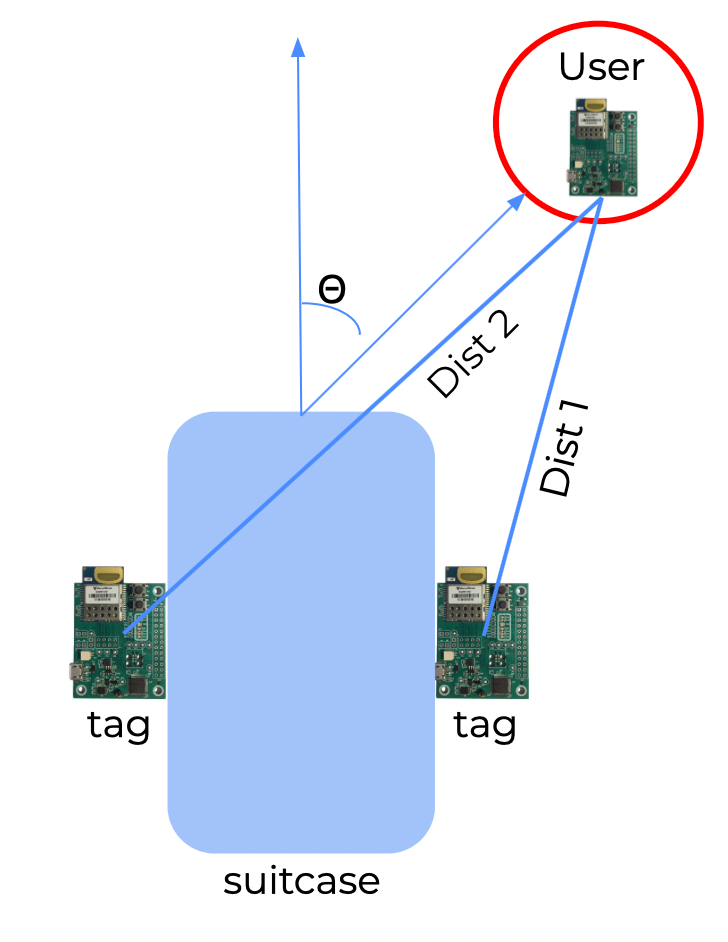
Lastly, to control our system, we use both an Arduino Mega and a Raspberry Pi 3B in communication. The Arduino receives obstacle detection input from the IR sensors and sends controls to the motor controller, DC motors, and servo motors. The Raspberry Pi receives distance readings from the UWB modules and communicates directly with the Arduino through the serial connection.
Ultimately, this allows for seamless and instantaneous communication between the "brains", or the UWB modules and sensors, and the "brawn", or the motors, of MASA.
VIDEOS
2D following of MASA (swaying is due to UWB noise)
Obstacle avoidance + 2D following of MASA
Back-up feature of MASA (if stuck in a corner)
FINAL PROJECT POSTER
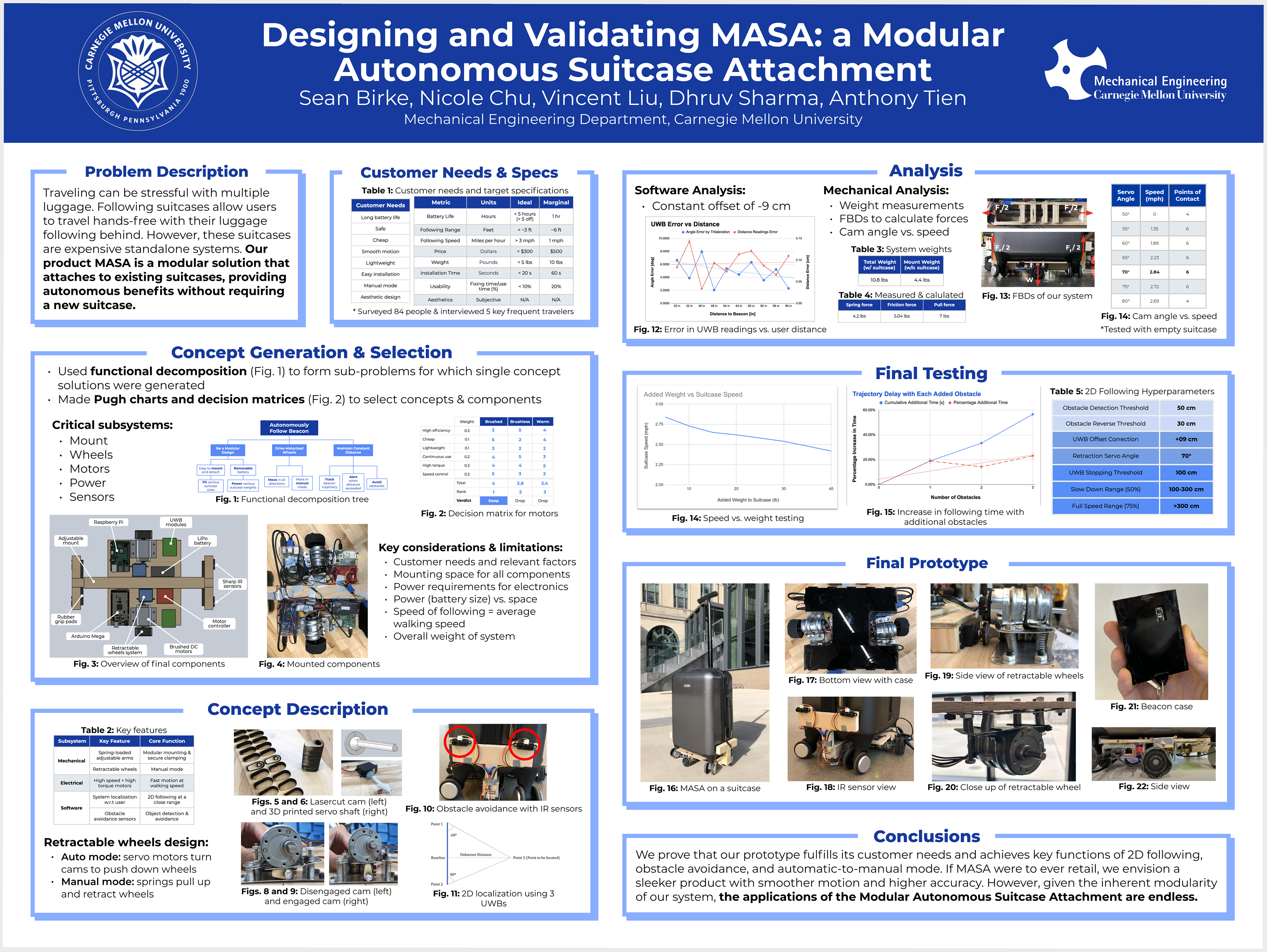
Final project poster